CO₂をパワーに変える!アイシンの「資源循環システム」が始動
2023.05.30
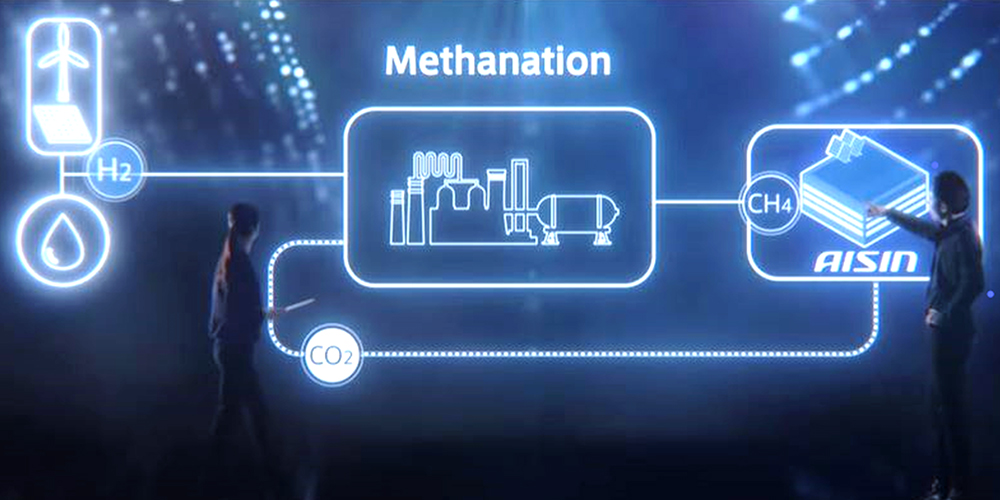
将来の世代も安心して暮らせる持続可能な社会をめざして、アイシンは「製品」、「生産」の両軸でのカーボンニュートラル(CN)を加速させています。
生産面では「動力源・熱源・無駄レス」、「クリーンエネルギー」、「廃棄物ゼロをめざした資源循環」を軸に技術開発を推進しています。その中で重要な開発テーマの1つと位置付けているのが西尾ダイカスト工場(愛知県西尾市)で評価をスタートした「資源循環システム」です。
「資源循環システム」は、工場の燃焼設備で発生する排ガス中に含まれるCO₂を分離・回収し利活用するシステムで、回収したCO₂からメタンガスを生成し、溶解炉の燃料として循環させます。2035年の生産CN実現に向けた主要なソリューションのひとつとして、開発者たちが挑戦を続けています。
アイシンがCO₂の利活用に取り組む理由
アイシンでは、主力製品のeAxle(イーアクスル)やトランスミッションなど、アルミを原材料とする自動車部品を多く取り扱っています。
アルミ溶解炉など燃焼設備では、都市ガスを中心としたエネルギーを使用します。燃焼時にはCO₂が排出され、その量は工場から出るCO₂の約4分の1を占めます。生産プロセスにおいて多くのCO₂を直接排出するアイシンにとってCNは社会的責務であり、カーボンリサイクル技術の早期確立は喫緊の課題となっています。
資源循環システムは、その有望なソリューションの一つとして2021年7月に開発プロジェクトをキックオフ。始動から1年9カ月というスピードで、システムの評価開始までこぎ着けました。
CO₂分離・回収、利活用を行う「資源循環システム」
資源循環システムのしくみ
資源循環システムは、工場の燃焼設備で発生する排ガスからCO₂を取り出す「CO₂分離・回収工程」と、取り出したCO₂から天然ガス(LNG)の主成分であるメタンを生成する「メタン化工程」で構成されています。
工場のアルミ溶解炉から出た高温の排ガスは、まず排ガス回収工程で粉塵などを取り除き、常温まで冷やします。この段階でのCO₂濃度は5~10%程度と高くありません。続くCO₂分離・回収工程でCO₂濃度を99%まで高め、高純度なCO₂を圧縮し、タンクに貯蔵します。次のメタン化工程ではCO₂と水素を反応させ、メタンを生成します。生成したメタンは既存のガス経路に流し込んで再利用します。
「資源循環システム」フローイメージ
排ガス中のCO₂を回収し、生成したメタンを再び燃料として再利用するという循環を繰り返すことで、CO₂の排出量を大きく減らすことができます。
小型化・高効率・熱利用が特徴
「システムの鍵となるのは独自性の高いCO₂分離・回収工程」と、開発を担当する水間紘太郎は説明します。
「アイシンが採用したのは、吸収剤を使ってCO₂の分離・回収を行う『化学吸収方式』。そこに独自設計の回収機構と、その機構に最適な吸収剤を用いてCO₂の分離・回収を効率化することでシステムの小型化を可能にしました。化学吸収方式では一般的に高さ20メートルほどの大型設備が必要ですが、アイシンのシステムは約3メートル。実用化の肝となるコンパクト化と低エネルギー稼働性能を実現できたことで、実用化への視界が大きく開けたと考えています」(水間)
資源循環システム開発 水間紘太郎
もう一つの主要なプロセスであるメタン化工程は、メタンの生成だけでなく熱を再利用しているのもポイント。CO₂が水素と反応する際に発生する熱をCO₂分離・回収工程に循環し、吸収剤の加熱に使っています。将来は溶解炉からの排熱もCO₂分離・回収工程に利用することで、通常なら捨てられてしまう熱をムダなく再利用し、システムのさらなる効率化を図ります。
多様なメンバーでスピード開発
プロジェクトには組織の壁を越えてさまざまな部門から技術者が集結しました。液体循環にはクルマで採用されている電動ポンプや、熱マネジメントの技術が生かされています。システムの小型化、効率化は生技部門の得意とするところ。開発プロジェクトを率いる松本晃和は「CNという一つの目標に向かい、部署間の壁を越えて一丸となれた。金属加工から設備、化学系までモノづくりの幅広い技術とノウハウがあるのがアイシンの強み。グループ企業や取引先も含め、さまざまなバックグラウンドを持つメンバーが協力し、地道なステップを踏みながら短期間で評価までたどり着けたのがアイシンらしい」とチームワークの良さを強調します。
資源循環システム開発 松本晃和
課題を“見える化”
評価を開始したシステムのCO₂回収量は、0.024t-CO₂/日、メタンにして12㎥/日(ntp※)相当。これは、溶解炉1台から発生するCO₂の約1/100にあたります。今回の評価で得たデータから、2025年度には溶解炉1台から発生するCO₂を全量回収するシステムの開発をめざします。
※normal temperature and pressureの略。圧力1気圧、温度0℃における気体の状態をいいます。
工場の排ガス排出量は常に一定ではなく、休憩時間や段取り時間など、さまざまな要因によって変動します。そのため、全体効率を維持しながら能力を100倍にすることは、かなり難しい挑戦になると考えられます。現在はシステムに取り付けたセンサーで、圧力や温度などさまざまな情報を“見える化”。課題を洗い出し、高効率で安定したCO₂の回収、再利用を追求していきます。
さまざまな方法で社会ニーズに応える
世界は脱炭素化社会に生まれ変わろうとしています。松本は「地球温暖化を防ぐ技術に携わるやりがいと責任感を、メンバー全員で共有しています。生産CO₂の排出量を下げることは、製品の競争力強化にもつながるはず。また、アイシンのように溶解炉を使い、CO₂排出量の削減に課題を抱える企業は少なくありません。将来はグループ会社への導入も視野に、他社のCO₂低減も支援できる技術開発で、社会に貢献していきます。」と意気込みを語ります。
アイシンは2035年の生産CN、40年に地球環境と人にやさしいゼロエミッション工場の達成という高い目標に挑戦しており、今回の取り組みだけでなく水素燃焼装置やCO₂の固定化など多角的な技術開発を進めています。これは、複数の選択肢を持つことで社会インフラや燃料コストなど状況の変化に柔軟に対応し、最適な方式を選択できると考えているからです。
アイシンはこれからも地球環境を守り、社会ニーズに柔軟に対応できる技術開発を推進します。AI Thinkでは引き続き、その姿をお伝えしていきます。