工場の省エネ技術を磨き、カーボンニュートラルの実現へ
~アルミ溶解炉のCO₂削減に向けた取り組み~
2022.04.20
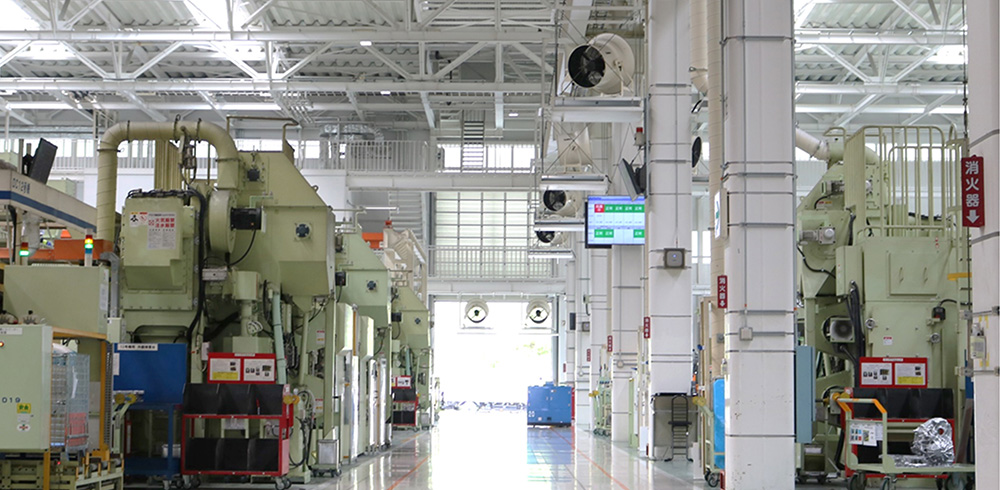
自然と調和し、誰もが安心して暮らせる社会の実現をめざすアイシンにとって、カーボンニュートラル(CN)は経営の最重要課題です。2030年CO₂50%削減、2050年カーボンニュートラルの実現に向け、「生産」と「製品」の両軸で取り組んでいます。
その生産面において、アイシンの国内全体のCO₂排出量の約30%を占めるのが、ダイカスト、溶解炉、熱処理などの熱に関する工程です。これらの工程おけるCO2排出量を押さえていくことが、カーボンニュートラルの大きな成果につながると考えています。
「熱い・暗い」 従来のダイカスト工場のイメージを刷新
はじめに、皆さんはダイカスト工場と聞くと、どのようなイメージを思い浮かべますか?
ダイカストとは、溶かしたアルミなどの金属を金型に圧力をかけながら流入することで、高い寸法精度の鋳物を短時間に大量生産する工法のこと。アイシンでは、この工法によって電気自動車やハイブリッド車に搭載される電動ユニットのケースなどを成型しています。
こうした工程では、金属を溶かすために高熱を必要とすることや大きな設備を必要とすることなどから、工場内は熱い・暗いといったイメージを持っていないでしょうか?アイシンの工場においても、これまではそのような印象でした。
しかし、2018年に稼働を開始した西尾ダイカスト工場南棟は、天井からの自然採光を取り入れ、断熱や換気、さらには内装を白色にすることで、従来のイメージを払拭する職場環境を実現しています。さらに工場の屋根には、約1,000kWの発電容量の太陽光パネルを敷き詰め、再生エネルギーの活用にも取り組んでいます。
バーナーの燃焼を制御する技術でCO₂削減
アルミを溶かす溶解炉(左)と溶けたアルミを貯蔵する保持炉
アルミ溶解炉では、はじめに材料であるアルミのインゴット(かたまり)をガスバーナーで溶かします。その際、炉内の排ガスの温度を管理し、600℃以上になるとバーナーの出力を切っていました。従来、その出力はオンかオフ(0か100%)の切り替えしかできなかったため、アルミが少量の場合は頻繁にそれを繰り返し調整していましたが、それでも無駄なエネルギーが発生していました。
そこで、西尾ダイカスト工場南棟の新たな溶解炉では、出力を25~100%で柔軟に制御できるようにしました。そして、炉内の温度や投入したアルミの状態をモニターで把握し、調整することで効率よく溶解し、無駄なエネルギーの発生を抑えています。現在は、西尾ダイカスト工場南棟内の全7炉への展開が完了し、2020年度のCO₂排出量は、2018年度比で15%低減できました。
このように、エネルギーの無駄を排除する技術は、今後どのような電源構成になっても必要な基本の技術です。アイシンはその技術に磨きを掛け、他工場を含めたほかの炉への展開を進めています。
その先の技術の実用化に向けても、開発の手は緩めません。
2025年には、溶解前のアルミを電気エネルギーで予熱することでガスバーナーの使用を抑えるとともに、現状の2段構えになっている溶解炉と保持炉を一体化することで、CO₂排出量37%低減(18年度比)をめざします。
さらに、水素やCN燃料の将来的な活用も視野に、すでに実証実験に取り組んでいます。
プロジェクトを推進する軽合金生技部の鵜飼は、次のように意気込みを語ります。
「CO₂削減のハードルは高いです。将来に向けた技術の実用化には、初期投資の抑制や効率改善など、より一層の技術開発に向けた挑戦が必要です。しかし、“未来に笑顔を”届けるために、その高いハードルに挑み続けます。」
工業炉バーナーの水素燃焼技術に関する東邦ガスとの共同実証実験の開始について
アイシンは、カーボンニュートラルの実現に向けた取り組みを、「生産」と「製品」の両軸で今後より一層加速させていきます。