クルマの電動化を切り拓く「ものづくり力」
~ダントツを追求するアイシンの生産技術~
2022.11.14
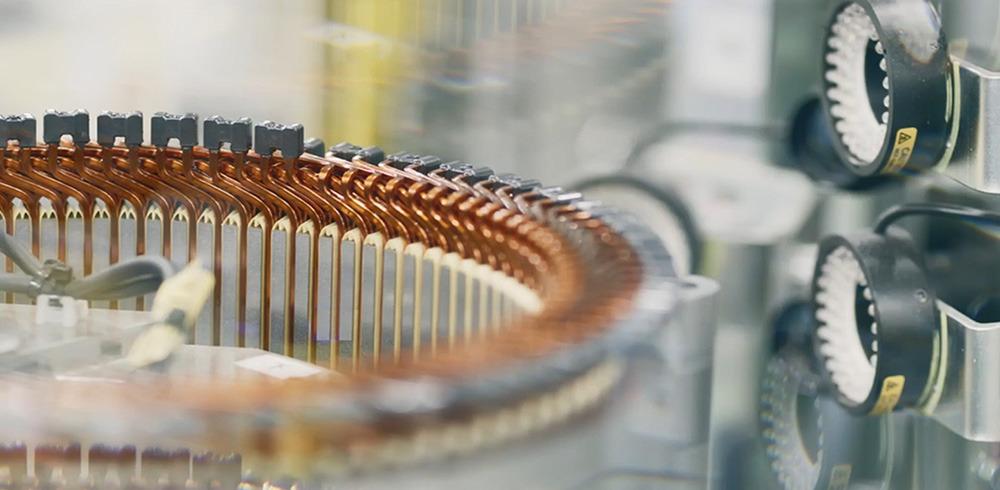
これまでの常識を超えた軽さ、薄さ、速さなど、世の中の人々があっと驚く性能を持って生み出されるさまざまな新製品。その誕生の背景には、新しい技術やデザインを“製品化”して世に送り出すために、工場の生産ラインの設計や生産設備の開発に取り組む「生産技術」という重要な仕事があります。
それでは、新製品を実現するために新たな生産技術が生まれるのか、それとも生産技術が進化してこそ新製品が生まれるのか、どちらなのでしょうか?
答えは、その“両方”です。新製品は、新たな製品設計と生産技術との両輪がかみ合わさってこそ誕生するのです。
世界中に広がるお客様のニーズにスピーディーに対応するために、ハイブリッド車や電気自動車(BEV)などの各種電動車に搭載する電動ユニットをフルラインアップでそろえるアイシン。今回は、その電動ユニットに関連する生産技術の「2つの挑戦」にスポットを当てました。
新たな「駆動モーター」の開発と量産化への挑戦
トヨタの新型クラウンに搭載された「1モーターハイブリッドトランスミッション※」は、新設計の6速オートマチックトランスミッション(AT)と駆動モーター、インバーターを一体化した製品で、高い加速性能と燃費性能に貢献しています。
※ BluE Nexus、デンソーと3社で共同開発
この製品において、クルマの走行性能を左右するといっても過言ではない重要な部品が「駆動モーター」です。駆動モーターは、電気を使用した“ハイブリッド走行”や“EV走行”といった走行モードで活躍します。1モーターハイブリッドトランスミッションでは、その駆動モーターをガソリン車に搭載されるATの「トルクコンバーター※」という部品が収まっていたのと同じスペースに搭載する必要がありました。
※ エンジンの動力を変速ギアに伝達する部品
厚さ10cmほどの非常に狭いスペースに駆動モーターを搭載する、それが今回紹介する生産技術の一つ目の挑戦になります。
はじめに、モーターの基本的な仕組みを紹介します。
モーターは、電力を供給すると回転力を発揮して何かを動かす動力を生み出すことができる部品です。内部は「コイル」と言われる電線で構成されていて、この電線に電流を流して回転力を発揮する仕組みになっています。
コイルをたくさん巻き付け、電流を流せば大きな回転力を発揮することができますが、そうするとモーターの体積が増えて搭載スペースや重量の問題が出てきます。モーターは、いかに電線を密度高く巻き付け、高出力を確保しながらも小型化できるかが求められているのです。
そこで、モーターの厚みを薄くするためにアイシンの開発チームが着目したのが、モーターの性能に関係しない「コイルエンド」(下図)です。
では、コイルエンド部分をどのように小さくすればよいのか?
これまでは製品設計(形状)を設計部署が担当し、その後、工程設計(工法)を生産技術部署が担当する“分業”が一般的な開発の流れでした。しかし今回は、生産技術を担うメンバーが製品設計の初期段階から開発に入り込み、「コイルエンドを小さくする」という同じ目標に向かって2つのチームが協力することで、設計時点から工法も見据えた新しい構造案を生み出しました。
最終的に採用したのが、溶接個所を低減することで円周方向へコイルを曲げ(溶接箇所を互いに干渉させない)、コイルエンドを小型化する方法です。(上図)
この方法を実現するために、コイルの形状や組み付け方も一から見直し、その結果コイルエンドの厚みを従来比で40%以上も薄くすることに成功しました。
さらに、量産して世に送り出すために加工設備も新たに自社開発。こうした新たな駆動モーターの開発に向けた一連の取り組みが実を結び、1モーターハイブリッドトランスミッションの誕生へとつながったのです。
“シンプル・イズ・ベスト” いろいろつくれる「混流生産」を可能にした電動ユニットの生産技術
これまで主力であったガソリン車に搭載されるATは、一つの製品がさまざまな車種に採用されるので生産数が多く、かつ一度採用されると次の新製品に切り替わるまでの期間も長いという特徴がありました。そのため、大量に生産することでコスト低減を図る大規模な生産ラインが適していたのです。しかし、電動車に搭載される電動ユニットは生産数が少量で、さらに数にも変動があるため、効率良く生産する必要があります。
生産技術のもう一つの挑戦、それは複数の種類の製品を一つのラインで生産することで効率性を高める「電動ユニットの混流生産の実現」です。
汎用かつフレキシブルな設備を使うことで多機種混流を可能にした組立ライン
アイシンでは、BEVの駆動源であるeAxle(eアクスル)を3機種(前輪用に150kWと80kW、後輪用に80kW)生産しています。これらのeAxleをそれぞれの独立したラインではなく、一つのラインで生産することを可能にしたのが、機種ごとの共通する工程を集約した全自動の「共通プラットフォーム」と、反対に機種ごとの異なる対応を可能にした「変動対応ライン」の2つを組み合わせた生産ラインです(上図)。
その共通プラットフォームには、ロボットアームの先端に装着する「ツール」を自動で持ち替えることができる組み立て機を新たに導入しました。従来はツールごとにロボットアームのセッティングが必要でした。これにより、1つのロボットで複数の加工を可能にし、混流生産に対応できるだけでなく、生産ラインのコンパクト化や導入するロボットの台数の低減などによるコスト低減を実現できたのです。
異なる種類の電動ユニットを順番に組み立てる“セル”
変動対応ラインでは、“セル”と呼ばれる一つの作業場で、次々と搬送されてくる異なる種類のeAxleを組み立てています。そこでは、一部のeAxleに必要とされる部品を取り付けますが、作業が完了した製品は再び共通プラットフォームに戻るような仕組みになっています。今後、現在の3機種のみならず、より多くの種類の製品を生産するようになっても、変動対応ラインの切り替えなどによって対応することができます。
これらの取り組みに加えて、工場内での製品や部品の搬送を担う自動搬送システム(AGV)を導入したり、IoTによるエネルギーの見える化を取り入れたりするなど、多くの新しい生産技術へ挑戦することで、生産ラインにおけるCO₂排出量30%削減(従来比)も達成しました。
こうした生産工程をシンプルにし、効率性を高める取り組みは、地球環境に優しいのみならず、海外の工場での生産ラインの立ち上げも容易にすることができます。世界中のより多くのお客様に環境に優しいクルマを楽しんでいただくために、今後はさまざまな地域で電動ユニットを生産していきたいとアイシンは考えています。
AGVで工場内の搬送作業を自動化
“移動”に感動を与える製品の背景には、技術開発と二人三脚で歩む、ダントツを追求するアイシンの「ものづくり力」があります。これからも、アイシングループ全体で世界中のお客様にさまざまな電動車に対応した電動ユニットを供給し、カーボンニュートラルの実現に貢献していきます。