Fusion of the Real World and Virtual World--New Manufacturing through DX
May.11, 2022
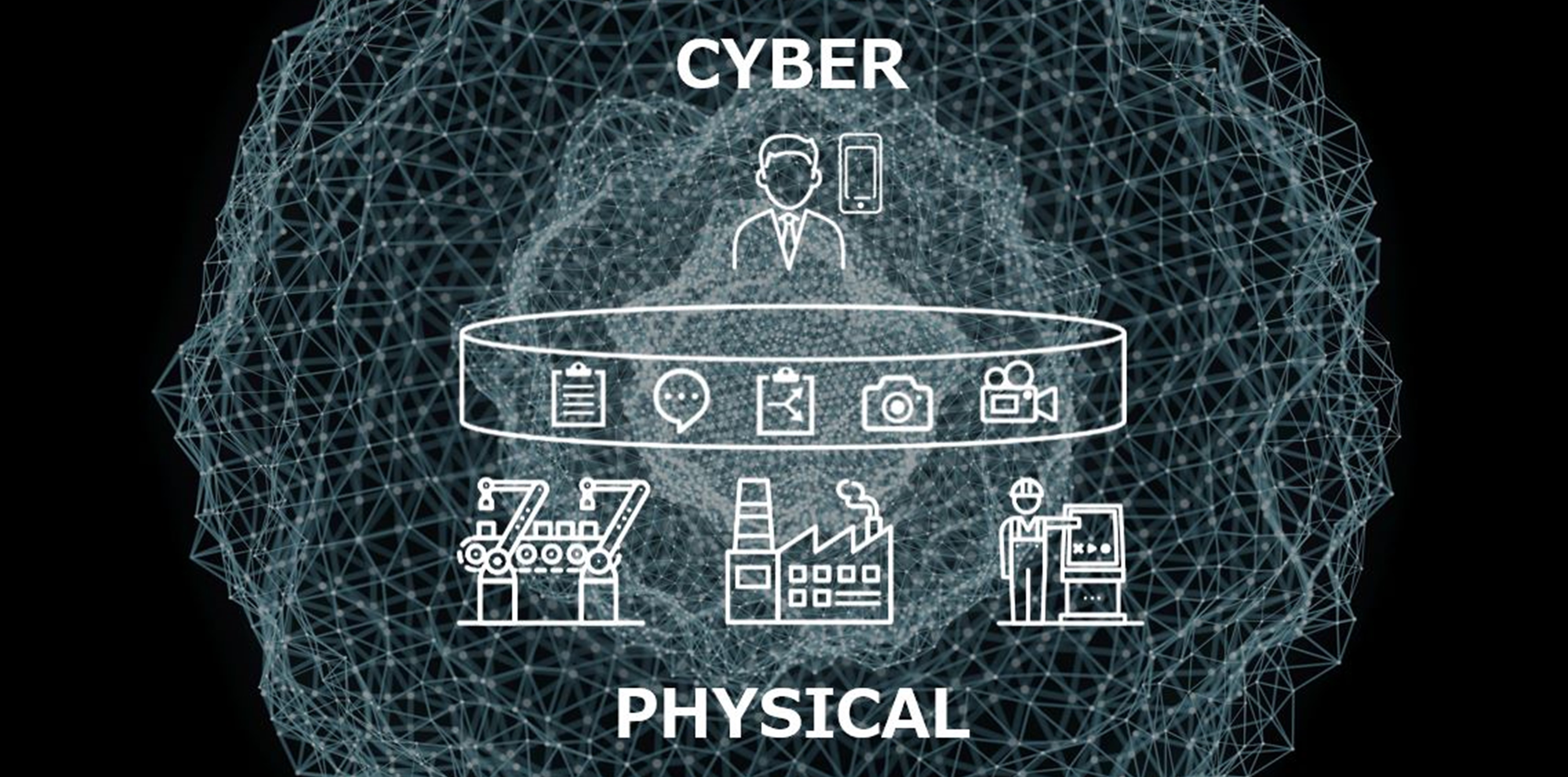
Internet of Things (IoT) technology connects everything to the internet, and advances in this technology are truly life-changing. A variety of things, ranging from home appliances to transportation, are connected to the Internet, making it possible to turn on the air conditioner remotely with a smartphone and check train and bus schedules in real time. With the growth of IoT technology, our lives will become more and more convenient.
It is said that if more things are connected to the Internet in the future, it will be possible to grasp in real time when, where, and what is happening. It may even become possible to reproduce the real world in virtual space based on the collected data.
Attempts are already underway in utilizing technology that reproduces the real world in virtual space for manufacturing.
How does a Cyber-Physical Information Factory virtualize the manufacturing process?
Aisin is promoting the Cyber-Physical Information Factory concept, a model that connects all workers and things in a plant via IoT and collects various information about them. With that information, we can innovate manufacturing through the reproduction of the entire physical plant in a virtual world.
Cyber-Physical Information Factory is a new manufacturing concept that aims to resolve issues and create new value by collecting information in physical space (the real world), analyzing the accumulated data in cyberspace (a virtual world), and then implementing the results back into to the physical space.
Aisin’s Cyber-Physical Information Factory is composed of the following three levels:
(1) Collection level
(2) Storage level
(3) Usage level
The data collected via IoT from the plant in the Collection level is aggregated in the Storage level. The data meeting a specific purpose is extracted, processed, and analyzed in the Usage level. The findings obtained there are fed back to the production process. The repetition of this cycle produces various benefits, including quick problem solving, quality and productivity improvements, and overall optimization.
The information collected from the Collection level is stored in the Storage level without any modification made to it. In the Storage level, a huge amount of data (big data) that represents actual production, including plant equipment and production processes/methods, is accumulated, whereby events that occurred in the actual plant can be virtually reproduced in cyberspace.
When an issue occurs, the cause can be identified through the reproduction of the past production status. Alternatively, highly accurate future predictions can be made based on the past production data by utilizing simulations and AI. The results will evolve the plant in physical space to a higher level. Aisin will realize such innovative manufacturing that fuses the cyber and physical spaces together.
Achieving a high level of efficiency and overall optimization by sharing information
An added benefit of the Cyber-Physical Information Factory is the sharing of information.
Previously, information was collected by application. Therefore, it was difficult to utilize such information for other purposes, resulting in insufficient cross-sectional cooperation.
For example, the Production Analysis Board used at production sites is a tool that visualizes the operational status of a production line by recording the performance of a process on an hourly basis, including the planned and actual production volume at the plant, and in the case of line stoppage, the cause, remedies, and influence on production.
The large amount of facility information collected to fill out the Production Analysis Board can be widely used for other purposes. However, the vertically-divided conventional system previously to hindered the cross-purpose use of the data.
Meanwhile, a Cyber-Physical Information Factory enables the data collected from the plant to be managed in the Storage level in an integrated manner. The data aggregated and processed in the Usage level can be used for various purposes, including production control, quality control, and traceability.
The central management and sharing of all information allow data to be used freely, regardless of application, making it easier to use the data for new purposes.
In the future, we will centrally manage production information as well as information on the entire business, including development, procurement, accounting, and personnel to achieve unprecedented levels of efficiency, overall optimization, and the creation of new value.
Streamlining production control with "Hancho Navi" that connects people to the network
The Cyber-Physical Information Factory enables all things that exist in a plant to be connected to the network. When humans are added to the connection in real time, the possibilities of manufacturing will expand dramatically.
Aisin has launched initiatives to streamline production control by connecting people, things, and information at a production site in real time with its proprietary web application "Hancho Navi," a navigation tool specifically designed to maximize efficiency for production line leaders.
At our plants, the person in charge of a production line is called "hancho" (Assistant Supervisor). The work of hancho is diverse, including helping other workers, responding to abnormalities in equipment, and filling out forms - tasks that take away from high value-added work, such as providing education and making improvements.
Observations of hancho’s movement revealed that they spend a considerable amount of time traveling. They go back and forth many times from one place to another - the production site, the form storage area, and the office - in order to respond to a call from the production site, deal with equipment abnormalities, fill out forms, enter data in a computer, and print documents.
Hancho Navi, a navigation system for Assistant Supervisors, was created to minimize the burdens on hancho and to allow them to best focus their time and energy toward maximum production.
If you access the Cyber-Physical Information Factory network with your smartphone or another familiar smart device via Hancho Navi, you can check the Production Analysis Board, read forms and operation manuals, and enter data anytime, anywhere. In addition, when an abnormality is detected, the equipment will automatically send a notification to your device. An action flowchart will be displayed on the screen to support prompt action. Furthermore, in conjunction with a chat tool, you can share text messages and images taken with the camera on your device with all concerned parties simultaneously. In this way, Hancho Navi can make communication livelier and more efficient.
Hancho Navi is not only for hancho (Assistant Supervisors) but for ALL plant workers. In the future, we will accelerate our initiatives with the aim of introducing Hancho Navi to all plants including those of our Group companies.
Real-time information sharing by connecting everything via IoT enables the optimization of the entire production process, increases efficiency, improves quality, and reduces costs. Moreover, it can evolve manufacturing itself, creating value that has never before existed.
Aisin is making great strides toward the realization of the extremely promising Cyber-Physical Information Factory. We will continue to revolutionize mobility by creating new manufacturing technology and opportunities through DX.