Introducing "Factory View," a virtual look inside Aisin factories
Nov.28, 2023
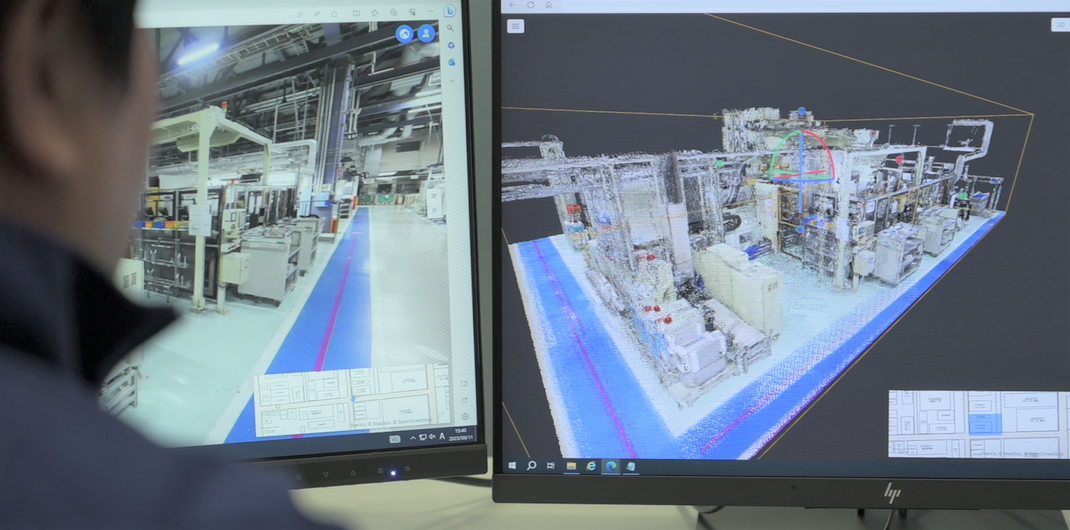
The automobile industry finds itself in the midst of a turbulent period in which the concept of cars is said to have been fundamentally overturned. Aisin is taking on the challenge of innovating manufacturing through DX (digital transformation)to promptly respond to social needs including electrification and the newly introduced IT tool “Factory View” is expected to be used more widely in the future. The main feature of this tool enables the user to freely look around in a factory -- even from a remote location. It’s also expected to improve development speed and productivity. Here, we will share the perspectives of our project members as well as the various functions of Factory View and our initiatives.
Digitally and remotely viewing factories
Factory View is a tool that uses images and point cloud data to recreate a factory in virtual space, allowing users to virtually see the inside of the factory, very similar to the benefit Google Street View* provides. By accessing the portal site from a computer, users can freely move around factories in Japan and overseas, and view desired locations and equipment in nearly all directions from anywhere at any time.
*Google Street View is a trademark or registered trademark of Google LLC.
Ryota Sakai, a project member, talks about the joy of Factory View:
“The biggest advantage is the remote aspect, enabling users to view factories from anywhere. For example, when discussing equipment relocation, we found things on-site that weren’t shown on the drawings, such as fire extinguishing equipment, manholes, and material storage areas. To prevent this, we used to physically check the site many times, which required many hours and repeated trips to the factory. The ability to preview factories online has enabled us to significantly reduce the number of trips between factories as well as the frequency of rework.”
Converting the entire factory into data to solve problems
The original purpose of launching Factory View was to reduce the burden of travel for employees. As the company responded to changes at a rapid pace, building new factories to address increased production volumes and restructuring itself due to management integration, engineers’ trips between factories dramatically increased. With less time available for existing job responsibilities, they had to further increase the speed of their work in order to cope with the rapid changes and increased responsibilities.
While seeking a way to solve this problem, Yoshiyuki Kawasaki, who led the project, came up with a method to “digitize the entire factory.”
The measurement device used is manufactured by NavVis, a German company, and enables quick and efficient data acquisition. A worker wearing the device can acquire images and point cloud data simultaneously by walking around in a factory.
Kai Matsumoto, who was instrumental in the initial launch, says, “Aisin is the first Japanese company to introduce NavVis’s system. Everything we did, from formulating operational rules to creating a portal site, was like navigating uncharted territory,” in looking back on the challenges the team faced back then. Currently, Hirotoshi Honda, who succeeded Matsumoto, has already completed the imaging at 19 plants in Japan. “Aisin has too many plants to measure by a small number of people. To ensure smooth progress, we also focused on training other members at various locations to enable them to use the device.” he says.
Responding to social needs by enhancing manufacturing efficiency
Factory View was a solution inspired to reduce the burden on employees, but expectations are growing for its expanded use as the environment changes.
The acceleration of the vehicle electrification process and shifting needs of the world toward electrified products will demand shorter cycles for the replacement and introduction of production lines. It is no exaggeration to say that the key to competition is how quickly a factory layouts can be changed and new lines installed. Improved manufacturing efficiency will also speed up product development, allowing faster response to diverse social needs.
The strength of Factory View lies in the simultaneous acquisition of images and “point cloud data,” which represents space or objects as a collection of points. It also enables 3D models to be created based on this data.
In other words, it is possible to recreate an entire Aisin factory using a 3D model. Advanced simulation is created when the factory model is combined with 3D models of the equipment and production lines, . The IT tool allows the user to verify productivity and in-factory logistics before a production line is installed in a factory, leading to a reduction in production preparation time.
Becoming an important tool in advancing manufacturing DX
The use of Factory View may be expanded and used in overseas plants and group companies, where significant cost and time saving benefits can be expected. The system can also be used as a Business Continuity Plan measure in instances such as damage caused by large-scale earthquakes and other natural disasters.
Kawasaki says he hopes to use Factory View for collaboration between factories. “We can expect Factory View to play a variety of roles, including improving efficiency, and I want it to serve as a small ‘observation window’ that helps workers share information between factories. Aisin has many factories around the world and produces a wide variety of products, which also makes me concerned about fragmented workplaces. I hope the system becomes a tool that helps workers learn from and correct abnormalities or areas of improvement by peeking into factories facing similar issues.”
Factory View can be used in many ways in addition to those introduced here. The system is drawing increasing attention and raising expectations as a tool that will become an important element to further advance Aisin’s manufacturing DX.