ロボットによるピッキング、ですか?
K.N : ええ。アイシンの工場では、たくさんのロボットが製品の組み立て作業などを行っているのですが、依然として多くの人間がそのサポート役を担っているのが現状です。私が自動化を担当しているピッキング作業もそうです。
ピッキングって部品を取って置くだけの作業ですよね?
K.N : はい。人間がやれば誰にでもできるような簡単な作業ですが、ロボットにやらせるのは実はかなり難しいんです。
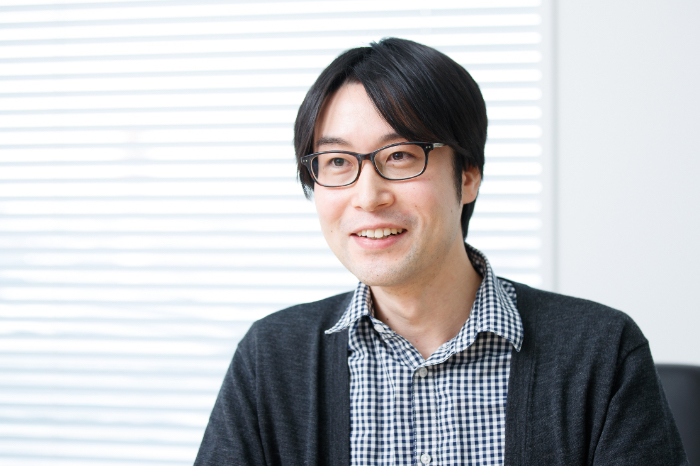
そうなんですか。では、改めて作業の流れを教えてください。
K.N : まず、ネジなどの部品が箱にごっそり入った状態で組み付け用ロボットの周辺に届きます。それを人間が箱からひとつずつ拾い出して、向きを揃えて一定間隔でトレイに並べるんですね。そうしないとロボットが組み付けられないんです。
部品を画像認識し、ピックアップし、一定間隔に並べる、ですね。難しいのはどこですか?
K.N : 箱の中に無造作に入れられたたくさんの部品の中から、それぞれの位置と姿勢を割り出すのが結構難しいんです。似たような形状が複数ある部品だと、姿勢を見間違えることもありますしね。
なるほど。それをいかに正しく認識させるかってことですね。
K.N : はい。ピックする部品の3DCADモデルを事前に読み込ませて「こことここを把持させて拾い上げる」というプログラムを事前に仕込んでおきます。この情報をもとに、箱の中の部品を三次元ビジョンで認識させることで、見間違いを防ぎながら拾い上げる制御につなげるわけです。2次元の画像ではなく3次元の点群として部品を捉えるイメージですね。

ピックアップの部分はどうです?
K.N : ピックアップ、つまり拾い上げる機能が一番難しいかもしれません。画像認識後、大量にある部品のどれから拾うかということを考えるのですが、ピックするときに部品の中に手を突っ込み、ロボットのハンドを壊してしまうことだけは絶対に避けないといけません。そんなことになれば生産が止まってしまいますからね。
いちばん上から取ればいいような気がしますが?
K.N : それが意外と難しくて、部品がごちゃっと入っている箱の中で「一番上の部品」を認識できないケースが稀にあります。画像認識の際に、部品全体が見えているものに最も高いスコアをつけて取りやすさの順位づけをしているのですが、干渉が発生する可能性があります。いかに干渉させずに拾い上げるか。ここが気を遣う部分ですね。
これら難題を克服してまでピッキングの自動化を目指す理由は?
K.N : 第一に、貴重な人的資源を守ることです。ピッキング作業に従事する方は一日中単純な作業を行わなくてはならないですし、部品の中にはひとつ10kgあるような重い鋳造品もあります。毎日繰り返し運ぶうちに腰を痛めてしまう可能性もあります。自動化の推進により、ピッキングに従事する社員に創造的でやりがいのある仕事に移ってもらうという狙いを持っています。
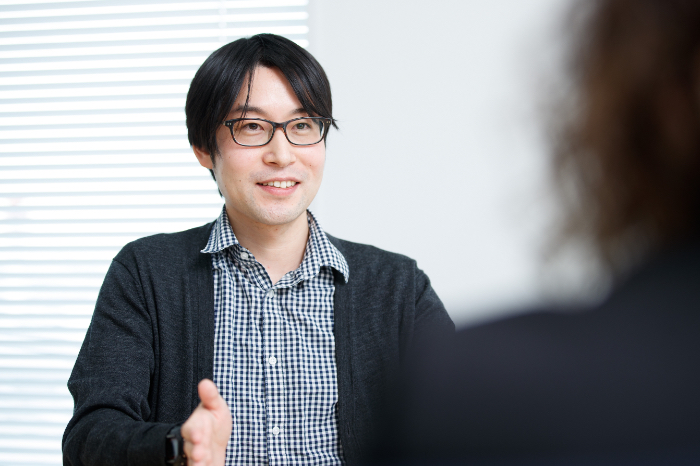
次に?
K.N : 第二に、コスト面です。ロボットピッキングを容易にする「パーツフィーダー」という装置は既に市販されているのですが、非常に高価である上、対象部品が変わるたびに費用を投じて装置ごと作り直さないといけません。そこでパーツフィーダーを必要としないピッキングシステムを内製化することで、コスト競争力を高めるというのが目的もあります。
「人間の役割をAIやロボットに」といってもやはり簡単ではないのですね。
K.N : 画像認識などサイバー世界で完結しているものは、まだいいんです。フィジカルな動き、つまり現実世界の作業ですね、これが入ってきた途端に難しくなるんです。ただ、現在は画像認識のみAIを使っていますが、将来的にはピックアップ時の制御もAI化できると思いますよ。自分で把持してみて、一番いい掴みどころを学習していくとか。
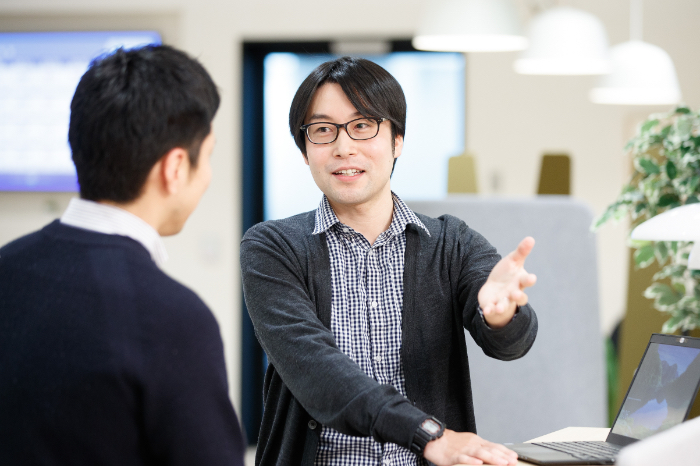
AI開発におけるアイシンの特色とは?
K.N : アイシンは工場で実際のモノを扱う機会が多いため、ピッキングロボットなどフィジカル面を含めた知能化技術を磨きやすい環境にあります。そして、今後はこのフィジカル面を含めた知能化技術が重要になると思っています。この点は強みだと思いますね。
今後の夢や目標があれば教えてください。
K.N : 世の中のIoT化が進む中、今後日常生活のさまざまなシーンで私たちの持つサイバーとフィジカルの融合技術が役立つと思います。それを活用し、人々の暮らしを変えてしまうような技術開発がしたい。それが今の私の夢です。
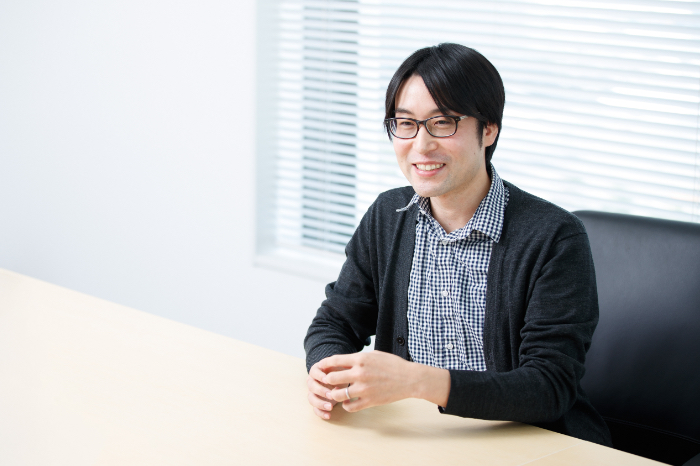